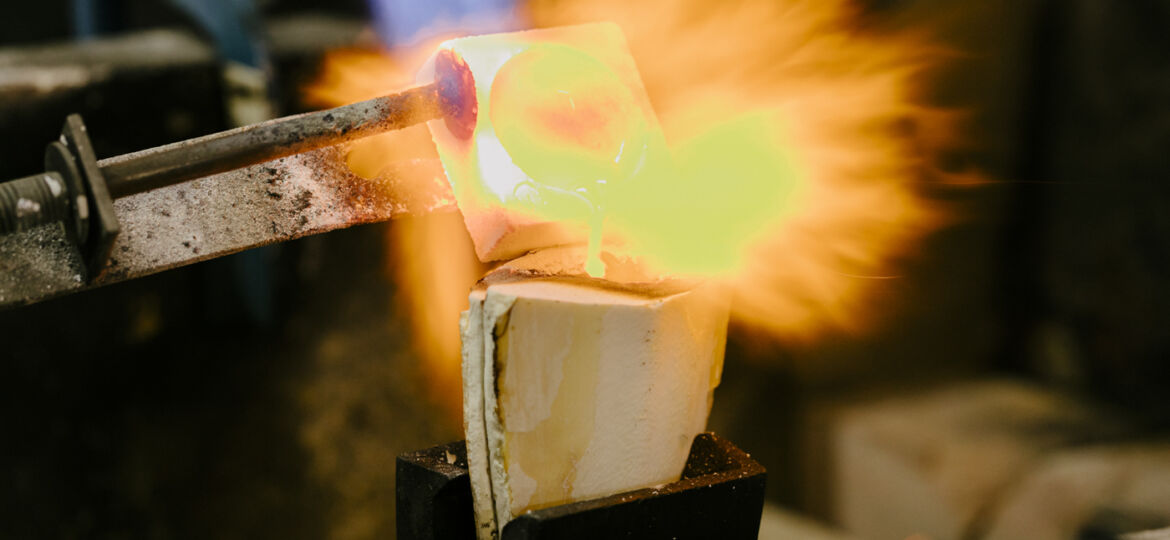
Let’s talk about techniques from the world of goldsmithing… And among the goldsmithing techniques of tradition there is one that, applied with great skill, allows jewelry to be given the status of a true work of art.
It is a family of related techniques, and based on a single principle, that of fusion, which succeeds in bringing different applied arts together, encapsulating their essence in a great piece of art jewelry.
Artistic craftsmanship, design, sculpture, and fashion thus come to be captured by a single creative process that literally fuses and fleshes out the idea, returning it as faithfully as possible and giving it new value.
Techniques belonging to the casting family begin with wax modeling, which is necessary to create the model on which the jewelry will be molded.
Even today, lost-wax casting techniques remain linked to the great traditions of the past, while making use of contemporary technical and technological knowledge.
The lost-wax casting process is used in the making of very complex parts and consists of preparing a model of the object that you will want to create and eventually reproduce, slightly enlarged from the actual size, in relation to both metal and wax shrinkage.
This model leads to the preparation of a shell-shaped casing, usually made of rubber, into which to inject a special wax.
Secondary models are thus obtained, which in turn are grouped together and mounted on wax supports until they form a more or less complex cluster of objects, complete with casting pans and funnels, which will allow the molten metal to fill every small crevice of the model. Clusters of wax objects are arranged within cylinders into which a special ceramic gypsum (scagliola) is poured, which, as it consolidates during firing, gives rise to the final shape from which the object is made.
While in the furnace, the removal of wax (hence the name “lost wax”) occurs, resulting in cavities with very smooth surfaces, perfect reproductions of the shape of the original models in negative.
The precious metal, previously melted in a furnace, is injected into the still-warm plaster brackets, thus acquiring the desired shape.
When the operation is complete, and once solidification has occurred, the plaster shells are broken up and any residual ceramic material is completely removed by appropriate washing. Having broken down the cluster into its individual elements with cutting wheels, the pieces are then finished and finished.